How Bob Evans Farms Makes America’s Favorite Mashed Potatoes
From field to table in a few hours, one plant in Ohio is responsible for nearly all of the company’s RTE mashed potato production plus millions of pounds of mac & cheese. Courtesy DronG / iStock / Getty Images Plus.
As the best-selling refrigerated side dish in the U.S., there’s a good chance they are on your holiday dinner table.
By Kelley Rodriguez
As the best-selling refrigerated side dish in the U.S., there’s a good chance they are on your holiday dinner table. A single plant in northwest Ohio produces about 136 million pounds of Bob Evans Farms RTE mashed potatoes, with automation and about 400 employees making the bulk of the brands’ mashed potatoes and macaroni and cheese, available in multiple flavors.
Bob Evans Farms, owned by Post Holdings, is based in a suburb of Columbus and known for farm-inspired mealtime helpers like RTE macaroni and cheese and breakfast favorites like sausage, ham and diced potatoes. Four manufacturing sites – in Ohio, Michigan and Texas -- handle production of the company’s RTE foods along with Post Holdings’ other brands, Simply Potatoes, Egg Beaters and Owens Sausage.
“We bring in truckloads of potatoes every day, right out of the field. We can (process) a truck load in about four hours,” said Chris Avery, director of manufacturing operations. “This facility has a ton of untapped potential – we’re capable of running 170 million pounds.”
The Lima plant processes over 2,300 semi truckloads of potatoes annually into refrigerated mashed potatoes. Courtesy Bob Evans Farms/Post Holdings.
As the best-selling refrigerated side dish in the U.S., there’s a good chance they are on your holiday dinner table. A single plant in northwest Ohio produces about 136 million pounds of Bob Evans Farms RTE mashed potatoes, with automation and about 400 employees making the bulk of the brands’ mashed potatoes and macaroni and cheese, available in multiple flavors.
Bob Evans Farms, owned by Post Holdings, is based in a suburb of Columbus and known for farm-inspired mealtime helpers like RTE macaroni and cheese and breakfast favorites like sausage, ham and diced potatoes. Four manufacturing sites – in Ohio, Michigan and Texas -- handle production of the company’s RTE foods along with Post Holdings’ other brands, Simply Potatoes, Egg Beaters and Owens Sausage.
“We bring in truckloads of potatoes every day, right out of the field. We can (process) a truck load in about four hours,” said Chris Avery, director of manufacturing operations. “This facility has a ton of untapped potential – we’re capable of running 170 million pounds.”
Over 130 million pounds of product is made at the Lima location annually, including about 115 million pounds of mashed potatoes. Courtesy Bob Evans Farms/Post Holdings.
During the mashing process, a propriety blend of dairy and spices is added, 1,500-pound batches at a time, using an automated system controlled by an employee. From the mixing process, the mashed potatoes are fed into a 4,000-pound holding tanks.
Automated packaging lines fill between 120-190 packages per minute, Avery said.
They are sealed and undergo checkweighing, and metal and foreign object detection before being wrapped in a cardboard sleeve and packaged in 9-count boxes for retail distribution. Case packing and forming is all done by robotics but palletizing is still manual.
After packaging, the side dishes into a spiral chiller to bring them down to refrigerated temperature.
Bob Evans Original Mashed Potatoes are the most popular flavor, accounting for 75 million pounds of annual production at the Lima site.
The plant holds about 300 pallets of finished product on site before sending it 80 miles south to the company’s distribution facility in Springfield.
“We try to turn the warehouse in 24 to 48 hours,” Avery said.
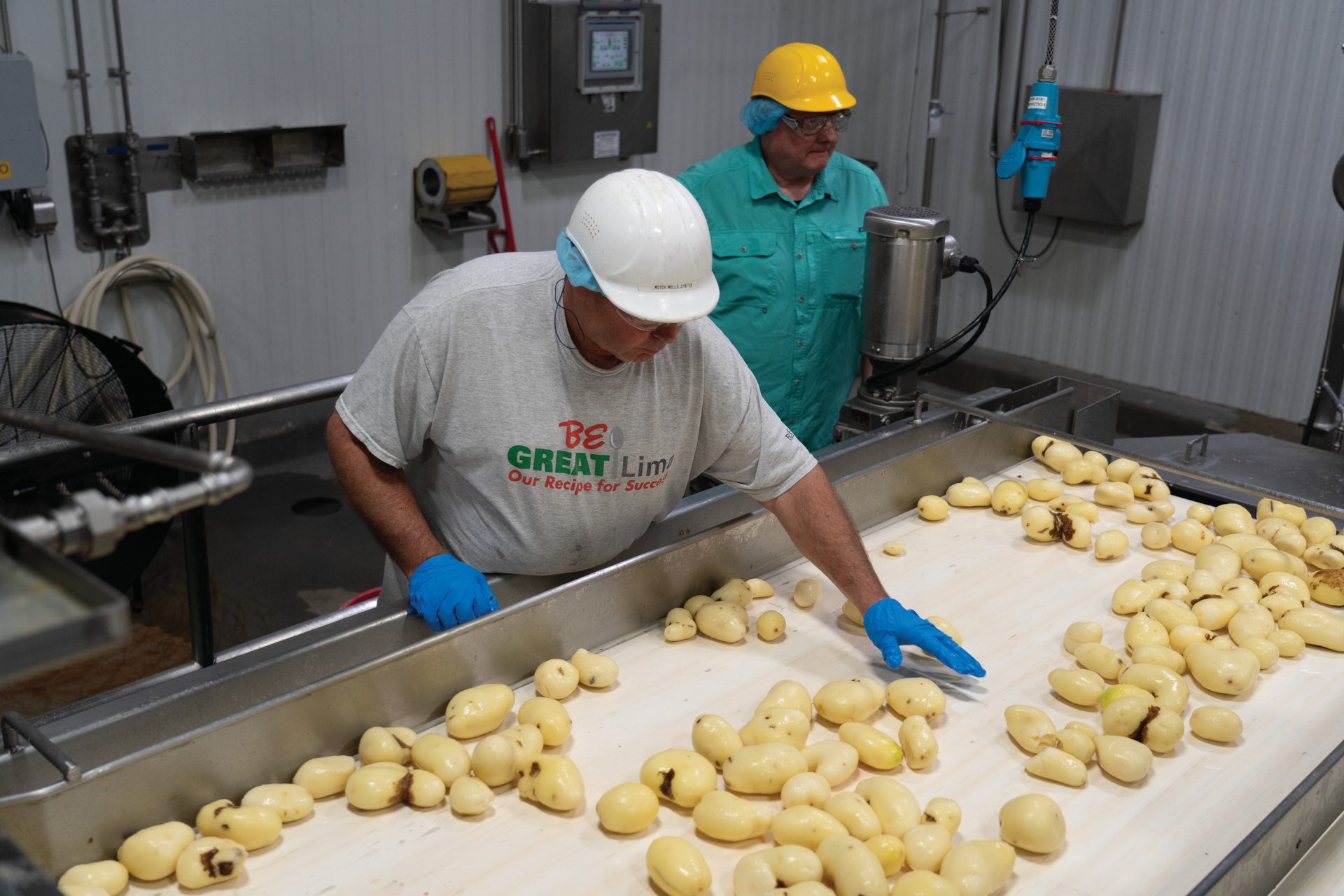
The Bob Evans Farms production plant in Lima, Ohio, produces over 23 SKUs of mashed potatoes and macaroni and cheese, employing over 300 people and automation across five production lines. Courtesy Bob Evans Farms/Post Holdings.
Upgrading lines or adding technology, like the robotic palletizing Avery said he would like to add at Lima, would require phases and happen in the early summer during incremental outages.
“We’d look at line priority and then built out a four-year strategy,” Avery said.
The plant runs three shifts, 24 hours a day, seven days a week. Avery credits much of the success to the staff.
“It’s really living our values of safety first – so people safety is of the utmost importance – so we’ll shut lines down if it’s not safe to operate and we encourage our employees to bring that to us, as opposed to a top-down approach,” he said. “The staff is very local. Our turnover, I think it’s less than 4% here and it’s just culture. The Bob Evans Management Operating System is really employee focused – it’s getting leaders on the floor, engaging with the workforce and helping them solve their problems to make their jobs easier.”
While the majority of throughput is mashed potato products for retail, the Lima location also produces about 20 million pounds of macaroni and cheese products annually, including retail and foodservice.